The Podsitive Impact of Meeting the Manufacturer
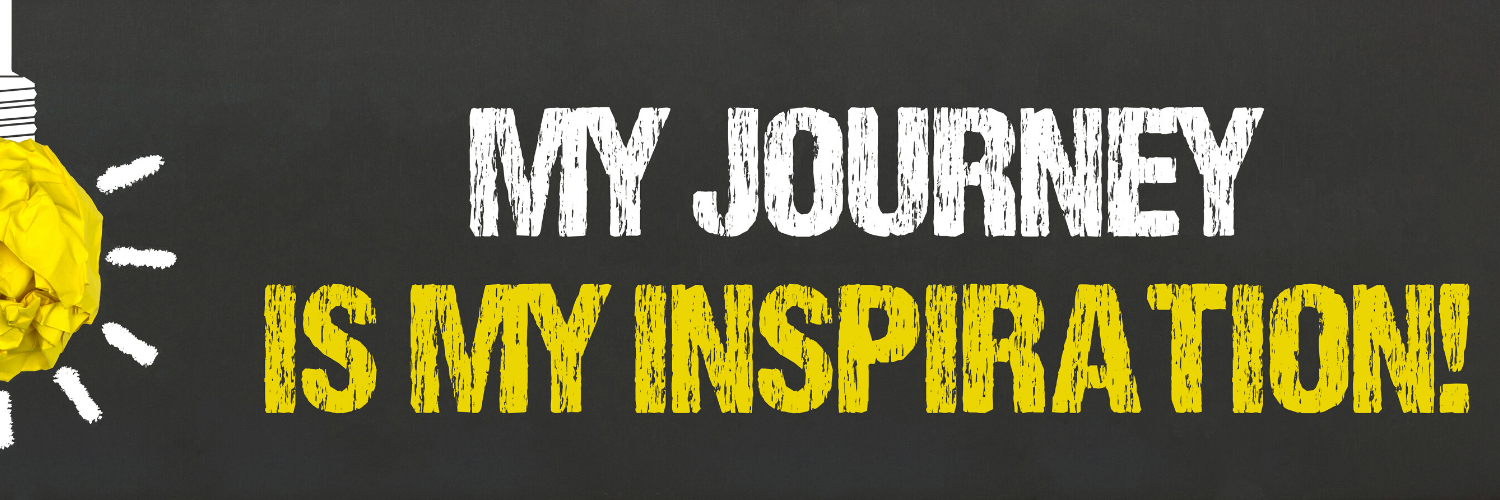
Life with type 1 diabetes means more moving parts, like test strips, glucose monitors, and insulin pumps to name a few. And then all those parts have parts!
The mechanisms inside my insulin pump have fascinated me for years.
In fact, before I even started pump therapy, my son and I took apart an Omnipod® Demo Pod (click here to order your own free Pod Experience Kit). But it proved quite difficult to do! Those durable little Pods are tough.
Once we did get inside, we found all sorts of stuff and were suddenly flooded with questions:
I mean, it was easy enough to figure out the basics. Inside the Pod is a reservoir for insulin, batteries, a needle and cannula, and whole bunch of other things like an incredibly complex circuit board. My awe of it all stemmed from my newness to insulin pump therapy.
After two decades of struggling with multiple daily injections (MDI), I made the switch to Omnipod. And I have never looked back.
But I did remain curious about where and how the Pods were manufactured.
It is no secret: I LOVE MY OMNIPOD. And I will share my experiences any chance I get.
When I was invited to speak at my first-ever Pod Therapy 101 webinar, I keenly watched the instructional video that shows the inner workings of a Pod. And I was pleased to see the assumptions I had made were correct: insulin reservoir, batteries, needle/cannula.
But several more questions popped up when I learned each Pod is made up of more than 70 individual components. Then even more when I found out about how and where they are made: in a clean room environment where the manufacturing process is fully automated.
This Spring, I received a special invitation to visit Insulet headquarters and the US manufacturing plant. It was a once-in-a-lifetime opportunity to enter a remarkable space and meet the manufacturing team.
But wait! I thought it was fully automated?
That’s right, there are actual people who show up every single day to make sure those robots are working properly and doing all the amazing things they are supposed to be doing.
Starting pump therapy is still one of the best life decisions I have ever made. The Omnipod System truly simplified things for me.
For years, I suffered through anxiety attacks at the hands of my needle phobia. And now, I can fill a Pod with insulin, attach it to my body, and let the automatic insertion do its thing. This is way better (for me!) than upwards of six daily insulin injections.
That little Pod is undoubtedly a feat of wonder and so is the US manufacturing plant.
When we arrived at headquarters, the buildings were streamlined and covered in solar panels. There were landscapers cleaning the grounds and planting flowers. The sun appeared to greet us just before we walked inside to begin the day.
Once inside we were briefed about the plant and the Pod making process. We learned about all the precautions taken so they could continue making Pods during the pandemic while other manufacturing plants were forced to close.
That’s right. All the Pods made during the pandemic were made at this facility. This means there was a dedicated group of humans who went to work, day in and day out, to make sure Podders could stay stocked with Pods.
I can’t even imagine what I would have done without Pods.
Before we dressed to enter the clean room, I was hit suddenly by an overwhelming feeling of gratitude.
We were the first “outsiders” invited into the space. The air in the room is cleaned 25-30 times an hour, and nothing in the clean room is ever touched by human hands.
Even though there are plenty of humans around.
They have the all-important job of making sure those automated processes are occurring and correctly. Over 100 automated quality inspections happen during the production of a single Pod! That ensures the absolute highest quality and performance of the device.
Watching it all happen was amazing! There were so many moving parts, all varying in size, all working together to create something incredible: a Pod.
Tens of millions of them (each year), actually!
The day truly was a one-of-kind experience. Kind of like each Pod.
And each person on the manufacturing team.
The morning spent in research and development, making a Pod, gave me a clearer understanding of why and how all those components work together. Seeing it come together piece by piece set the stage for what I would experience in the clean room.
But nothing could prepare me for sitting in front of the hundreds of people who show up each day for a live Q&A, so I can sit here and share with you. Because without them, there wouldn’t be a Pod for me. Or you.
We sat before them and shared our experiences, what it meant for us to wear a Pod. Of course, things became emotional quickly: a section of the room was dubbed The Crying Corner.
An insulin pump is such an intimate thing, it becomes a part of you (or least it, that’s how it feels for me). And mine changed my life.
So, I thanked them. And told them how grateful I was.
Because they all play a role in that change, and in every Pod I wear.
At the close of the day, we were given a transparent Pod to commemorate the experience. It was a unique gift to end a unique day.
And for me it, like every Pod I wear, is a reminder of all the people tied to all the moving parts inside and processes that made it.
A beautiful medley of science, technology, and humanity.